Why Is This So Important In Major Industry?
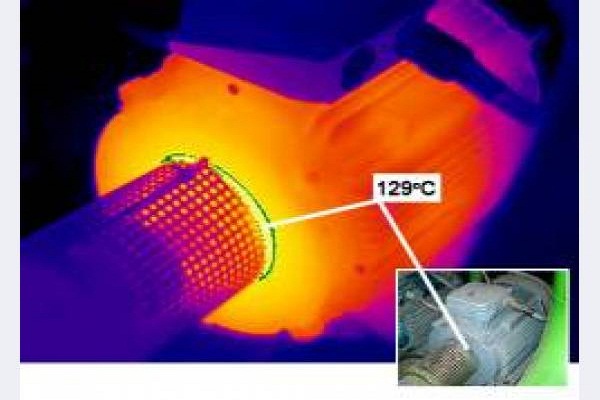
Abnormal heat signatures are often the sign of a piece of machinery that is malfunctioning. Often there is too much friction being generated between bearing and couplings on a rotating system, and this leads to heat.
This friction is the sign of a machine that isn’t performing smoothly and has developed a fault. Undetected faults could then develop into a much larger problem that is more difficult to fix and potentially more dangerous for those involved.
This use of thermal imagers can be used to great effect in some areas. These include overloaded electrical systems, blocked fluid systems, poor insulation in low slope roofs and a range of mechanical systems.
It can be difficult to detect problems in rotating equipment, pumps and motors without the use of these thermal cameras.
Using Thermal Cameras For Predictive Maintenance In Rotating Equipment
There is the chance that companies are already aware that there is something wrong with their rotating systems and simply need to locate the cause. Thermal imaging is the best option because it helps to highlight problem areas. Motors and pumps are complex devices.
It can take just one small error in one small element to start a chain reaction of issues. Technicians that locate that small starting point through an abnormal heat signature can diagnose the problem more easily. The most significant benefit of thermal imagers, however, is predictive maintenance.
This means regularly checking equipment to spot any abnormalities before they become a problem. A high-end thermal camera system can provide detailed images of the area and store previous data for comparisons.
Why Is This Predictive Maintenance So Important For Companies?
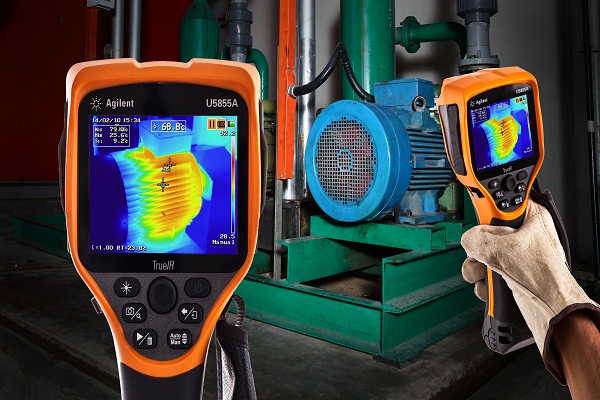
The importance of these thermal images in this industry cannot be over-emphasized because of the impact that these finding can have. It pays to identify issues as soon as possible to be sure of low-cost maintenance, efficient repairs, and worker safety.
One overheated element can be located, repaired or replaced with minimal cost or time lost. It is much easier to lubricate an overheating bearing if it caught early than to replace it when it breaks.
Problems that are left to build can spread and cause further problems. The machinery could become slower and less efficient, decreasing the effectiveness of the operation. These rotating parts also could become damaged further, leading to more difficult and more costly repairs.
There is also the issue of the longevity of the equipment. Rotating equipment in pumps and motors is specialized and costly. Companies do not want to be replacing systems if it can be avoided.
Thermal Imaging Predictive Maintenance Is Worth The Effort And Training
It can take the time to gain enough experience with these machines and their heat signatures to determine problems. Users need to understand radiometry, heat transfer and the necessary capabilities of this sophisticated equipment.
Sometimes the changes can be subtle signs of a developing problem, and they may not show up to the untrained eye. However, experienced users will spot the anomalies with ease. These images are therefore an important investment for saving time and money and potentially keeping workers safe.